Model-maker continually adopts new additive manufacturing technologies to meet market demands
- July 28, 2019
- Posted by: Chase Gregory
- Categories: Emerging Technology, Manufacturing
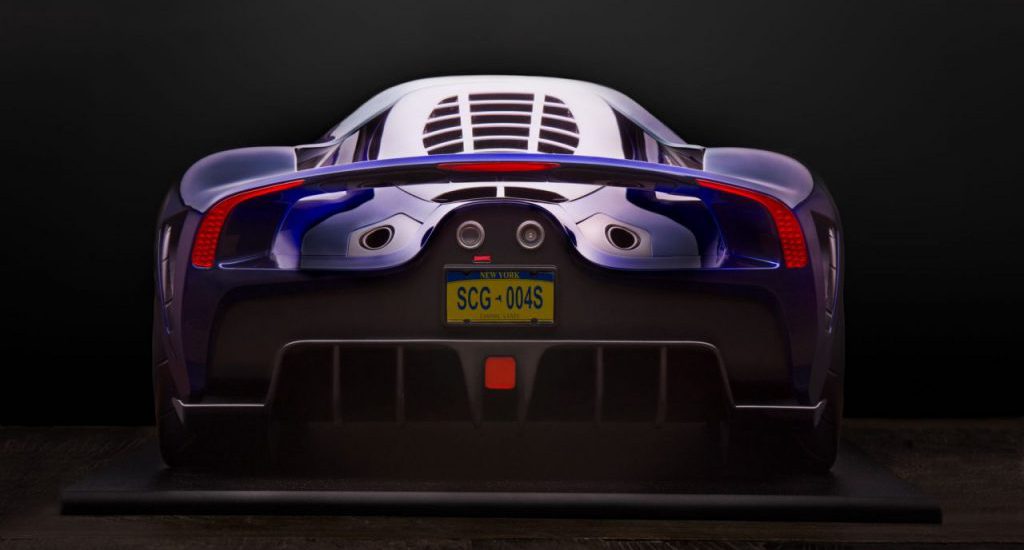
Aerosport Modeling and Design has been in business for 23 years, providing a wide range of services, including prototypes, appearance models, and working models; machines and reverse-engineers parts using scanning and 3D printing; and designing and building check and assembly fixtures. The company, which was founded by Geoff Combs, began as a basement operation but has since grown to include seven additive manufacturing (AM) systems, including UnionTech SLA, 3D Systems SLAs, Carbon M2, and HP Multi Jet Fusion (MJF).
In the early days of Aerosport, Combs would get his SLA parts from another shop, then finish them, make silicon molds, and paint them. But as the business grew, Combs purchased his first SLA machine in 2001, and he has since added more SLAs, as well as other AM systems. Today, the shop operates seven AM systems, one of which is a recently added MJF.
Aerosport Modeling designs and builds fixtures for a well-known jewelry manufacturer that uses the devices to hold rings and necklaces during laser engraving and etching operations. The shop found that it could 3D-print suitable production fixtures on the MJF. The technology allows building more intricate parts than an SLA, said the company’s prototype specialist, Steve Clark, because it eliminates the need for supports. The PA12 nylon used in the HP MJF has a higher flexibility than the prototype materials used in the SLA, allowing for many different snap fixtures.
Printing workholders has proved to be a big time-saver, too, compared to machining. Instead of taking five or six or eight or 10 days to machine all these little parts, the entire fixture can be printed overnight. Aerosport also builds assembly fixtures and go/no-go gauges for the automotive industry. Customers often ask for 3D-printed fixtures, partly because of the current buzz around AM.
Although 3D printing was stagnant for a while, Combs started to see orders coming in for a wider variety of additively manufactured parts about four years ago. Since then, the shop has been increasing its 3D printing capabilities to meet market demands. For purposes of comparison, Combs said an FDM (fused deposition modeling) printer might take 20 hours to build a fixture. “I can machine it in five. That being said, it’s way easier to just design the fixture, throw it on the printer, and walk away from it. Two days later, you come back and there’s your fixture.”
Aerosport Modeling also builds assembly fixtures and go/no-go gauges for the automotive industry. It’s common for customers to ask for 3D-printed fixtures, partly because of the current buzz around AM. And, according to Clark, “we have done some fixtures using 3D-printed parts. It usually depends on the application and time constraints. Often, it makes more sense to machine them out of (RenShape),” a machinable polyurethane board from Huntsman that can be used for production fixtures.
Early last year, Aerosport Modeling built a one-fifth-scale model of the Glickenhaus 004S racecar for Scuderia Cameron Glickenhaus (SCG), an American builder of racecars and limited-edition luxury sport cars. The model was produced using UnionTech SLA and HP MJF 3D printers. The MJF was used to print the more intricate parts of the model, while the SLA was used for larger parts.
In conclusion, Aerosport Modeling and Design’s success over the past 23 years has been built on its ability to adapt to new technologies and changing market demands. With 3D printing technology, the company has been able to expand its services and create products that are more complex and customizable than ever before. By integrating new technologies like HP Multi Jet Fusion into their processes, Aerosport has been able to produce fixtures and parts that are more durable, flexible, and cost-effective than traditional machining methods. As additive manufacturing continues to grow and evolve, it will be interesting to see how Aerosport Modeling and Design, and other manufacturers, continue to innovate and meet the needs of their customers.